Keep Kiln Turning with Proactive Lubrication Program
Kiln maintenance can be extremely difficult in cement, limestone, petroleum coke, and silica dust plants because of the harsh conditions associated with these industries. Lubrication Engineers has a long and successful track record providing solutions for the many lubrication-related challenges kiln operators encounter, such as heavy loads, temperature extremes, moisture, and particulates.
A proactive approach to kiln lubrication using a proven program can yield significant cost savings and help avoid unscheduled shutdowns. Lubricant selection is of primary importance, followed by putting in place lubrication reliability products and best practices to maximize the performance of the lubricant and protect the equipment. The right program will increase uptime; reduce gear and kiln wear; maintain kiln creep; lower lubricant consumption, waste disposal, and energy use; and contribute to a safer, cleaner work environment.
Lubrication Program Best Practices for Kilns
- Lubricate the kiln’s wear pads and tire bore using solid lubricant bars or spray grease.
- Select the best trunnion bearing lubricant to mitigate overheating, carbon buildup, and metal-to-metal contact.
- Implement an oil analysis program for gearboxes.
- Select the right high-performance gear oil for use in the gearbox.
- Implement a gear oil filtration program to 17/16/13 cleanliness code.
- Select the right high-performance open gear lubricant to maximize gear set operation and lifespan.
Identify Suffering Points & Move Forward with Our Proven Solutions
Kiln Wear Pad Erosion, Excessive Creep & Refractory Brick Loss
As the kiln rotates, the tire cradles the free-moving shell, resulting in immense pressure, severe friction, and metal wear. To mitigate potential damage, sacrificial wear pads protect the surfaces from each other. If the creep – the movement between both surfaces – goes beyond originally designed-for measurements, it indicates insufficient lubrication and can lead to metal-to-metal contact and erosion of the wear pads. Potential damage includes scoring, galling and cold welding of the kiln tires, wear pads and stop blocks, as well as loss of refractory brick.
LE Solution
Appropriate tire lubrication will ensure that creep is maintained by preventing the wear pads and shell from adhering to the tire. Easy Bar® with Almasol® brings together the wear-reducing benefits of LE’s proprietary solid EP additive, Almasol, with the proven benefits of Easy Bar solid lube bar technology. The bar’s patented blend of lubricants is suspended in a solid polymer binder that melts at approximately 49°C (120°F). The auto-ignition point of the bar is 538°C (1,000°F), which prevents dangerous flame-ups. When the bar is placed between the tire bore and shell, the binder melts, and the rolling action of the kiln distributes the lubricant where it’s needed to protect the surfaces and maintain creep.
LE Solution
If the Easy Bar with Almasol is unable to be used, a great alternative is Pyroshield Syn Kiln Grease (5190). Pyroshield Syn Kiln Grease features a high auto-ignition point and contains a synthetic thickener with organic and solid metallic film-forming components as well as Almasol, LE’s exclusive wear-reducing additive. The product’s high content of lubricating solids fills the surface imperfections, resulting in a smoother surface, lower friction and less wear.
Trunnion Bearing Overheating & Wear
Trunnion support roller bearings help carry the weight of the kiln and assist in rotation. Common challenges are severe unbalanced loads, overheating, metal-to-metal contact, lubricant starvation, and contamination. These can lead to excessive carbon buildup, bearing scuffing and pitting, and damage to the shaft.
LE Solution
Monolec® Syn Industrial Oil was designed to prolong equipment life by combatting the effects of high temperatures, contamination and heavy loads. It is formulated with high-viscosity synthetic base oil and an additive package that provides outstanding thermal stability, rust and oxidation resistance, and wear resistance.
Gearbox Oil Foaming, Overheating & Emulsification
Some gear oils foam and lose performance in the presence of moisture. Some are not able to maintain film strength when subjected to heavy loads, air or high temperatures. In this way, inferior or incorrect gear oil can lead to unnecessary wear and unplanned downtime. While OEMs recommend the viscosity and whether an EP package is needed, other properties are often ignored. Thermal stability, oxidation resistance, demulsibility, resistance to foaming, friction reduction, shear stability, tackiness, and film strength stability are all critical factors for gear oils.
LE Solution
Work with your local LE lubrication consultant to choose the Duolec® high-performance gear oil best suited to your application. LE’s Duolec gear oils are designed to combat the effects of high temperatures, water, contaminants and heavy loads. These superior quality oils will maximize equipment life.
Open Gear Wear
Open gears experience high-load, heavy-shock conditions and a dusty environment that can lead to surface wear like scoring, pitting and spalling. An inferior lubricant will not stand up to the extreme conditions. An extremely tacky lubricant with high film strength is needed.
LE Solution
Heavy-duty synthetic Pyroshield® Open Gear Lubricants exhibit exceptionally high film strength to provide outstanding protection for high-load, heavy-shock applications. Formulated specifically for open gear applications, they cling tenaciously to metal surfaces without accumulating; prevent metal-to-metal contact; and, in most cases, reduce gear temperatures.
Lubrication Reliability Program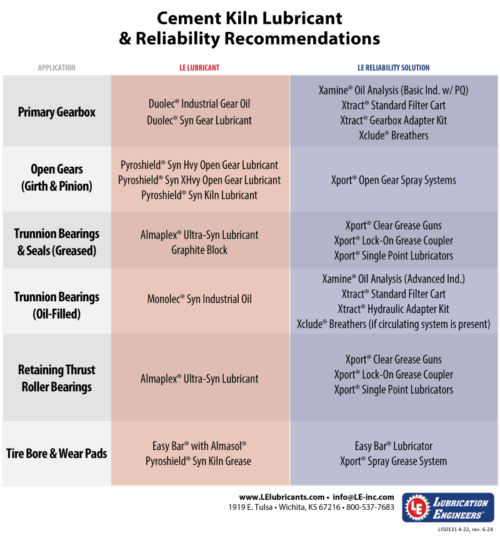
In conclusion, Lubrication Engineers can help put together a lubrication reliability program for your kiln applications to help them last longer, subsequently eliminating downtime and reducing maintenance costs.
Our certified lubrication experts can be onsite to help you put together a program. Start now by finding your local LE consultant or registering to purchase online.